Conveyor Application Challenges to Consider: Scalability, Expansion, Automation, and Integration
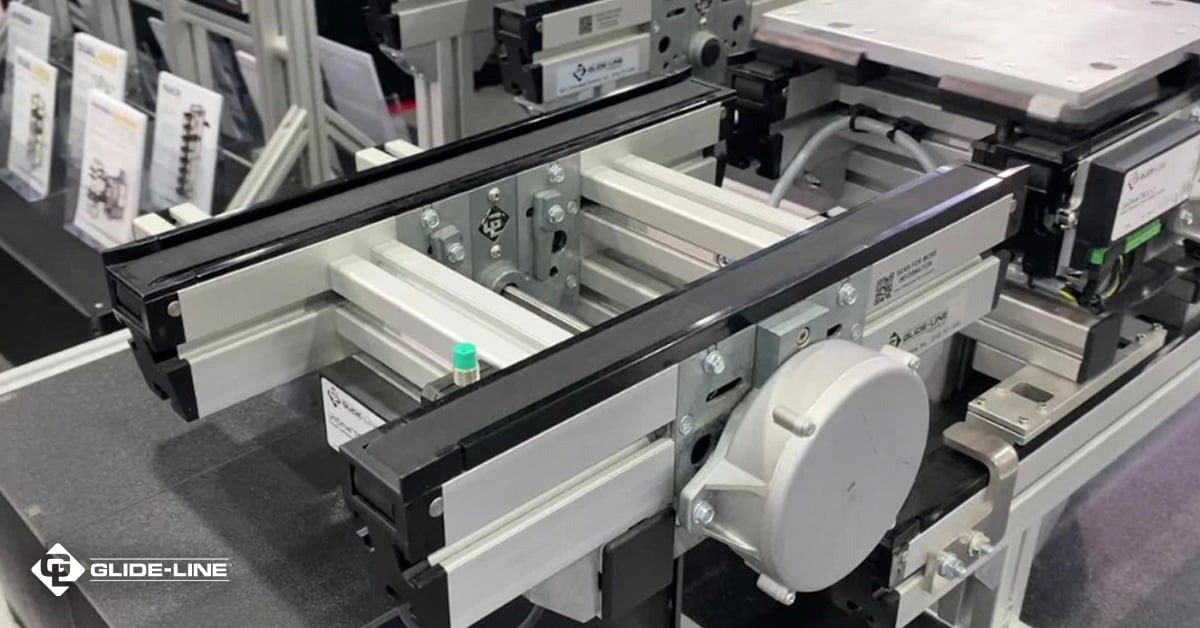
Designing a conveyor system that overcomes common challenges like scalability, expansion, automation, and integration is possible with the right manufacturer. Here are 5 ways you can solve your application challenges with a Glide-Line conveyor design:
1. CONVEYOR DRIVES, CONTROLS & ADAPTABLE CONVEYORS
One of the parts that everyone is struggling to find are chipsets and semiconductors required for AC drives. The variable frequency drives (VFDs) used in most conveyor designs aren’t easy to source, forcing manufacturers to look for alternative solutions that can perform according to the same design parameters these components offer. Choosing a solution that provides the drive control you need that doesn’t require a VFD or servo can help speed up the lead time when sourcing the system, eliminate concerns about spares, and reduce overall operating costs.
Glide-Line’s Zero Contact Zoned Conveyors use DC drives and controls to:
- Design a conveyor system with expandable sections that can adapt and grow with your manufacturing operation
- Provide smooth starts and stops while maintaining the required friction to move totes and trays on the belt
- Control the movement of each product pallet across different zones and prevent product collisions that lead to damage
2. TRANSFERS AND ELEVATION CHANGES
Moving products directly, pallets, totes and trays through different production stages may require vertical transfers, traffic control systems, or customized solutions to accumulate products. Integrating these functions with a tote or tray conveyance system could increase the physical footprint, create bottlenecks, or obstruct workers from accessing products. Eliminating curved direction changes, and automating vertical transfers are all possible with Glide-Line’s range of custom standard solutions.
The Glide-Line 360 product line provides you with expert material handling functionality including:
- A customizable solution that integrates with all other Glide-Line conveyors to move products efficiently through the facility
- 360° movements of product pallets including elevation changes and handovers to other conveyor lines for storage or accumulation
- Smooth handovers that don’t require additional space in the facility, allowing you to go over, under, or around other production lines
3. EXPANSION AND AUTOMATION
Expanding operations to meet future production demand should be a priority when choosing a conveyor for a specific product directly on the line, a pallet, tray or tote. Older systems may require more effort to automate or expand when your business needs change. Modular sections allow you to configure a new line when required, with limited disruptions to operations. Conveyance technologies have evolved drastically over the last two decades. Deploying a Glide-Line solution now will ensure you can grow operations, increase automation capabilities, and enable precise control over every item that moves through your facility.
Glide-Line makes automation easy with:
- Standard offering of conveyors and devices that integrate and interface with other manufacturing control solutions
- Modular and configurable solutions to adapt your conveyor line according to your current and future needs
- Different types of actuators, drives, belts, and control systems allow you to automate processes quickly
4. TOTE AND TRAY MANIPULATION
When workers interact with containers on the production line, you may have to manipulate the item to provide better ergonomics and ensure safe handling. In-line actuators could lift, lower, angle, or orientate totes according to the process requirements. Manipulating totes with bypass stations, sorting shuttles, accumulation buffers, or angled pedestals is easy when you integrate these systems with a Glide-Line conveyor.
To provide for the safe and efficient handling of totes, Glide-Line offers:
- Transfers and merge solutions that control the flow of products between process stages
- Lifts and pedestals that enable workers to access products at the right height and orientation when performing manual operations
- Material handling systems that can shuttle, merge, divert, accumulate, sort, stack, and store pallets according to your precise requirements
5. LEAD TIMES AND SYSTEM DESIGN
Another challenge isn’t just finding the solutions that can help you solve your unique application requirements, but sourcing it quickly. Once you know what’s possible and what you need to achieve your production goals, you need to design and build the system to maximize ROI and minimize disruptions. Application engineers have to be able to configure a solution, test its design in-context, and optimize the product flow around any existing infrastructure. Having a tool available to perform these activities, within existing facility models, will speed up the lead time, ensure accurate costing, and provide management with detailed information about the new solution.
With Glide-Line’s IMPACT! Configurator, you can:
- Quickly assemble a system design using a standard library of conveying components
- Place, move, and replace equipment within your existing SolidWorks CAD models
- Study different scenarios, find accurate pricing, and make changes quickly when you have to expand or adapt your design
Complex Application Challenges Made Easy
Glide-Line provides precise material handling systems that can scale with your production operations. For the fast and efficient movement of totes and trays, our timing belt conveyors give unmatched flexibility with the shortest lead times in the industry. You can assemble a system that solves complex application challenges and start your journey toward automated operations today.